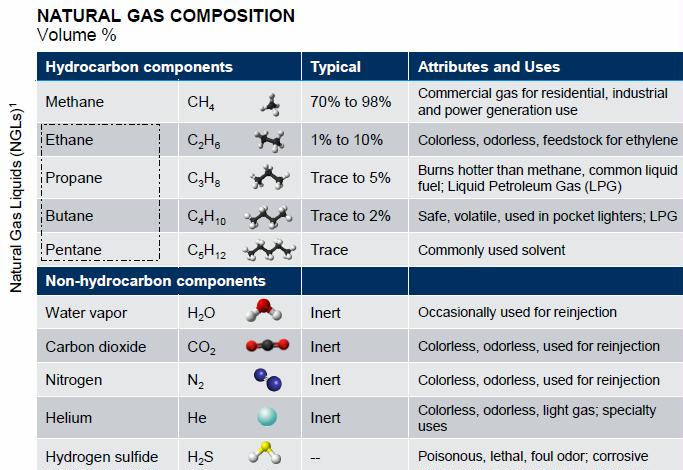
Impurities can also be present in large proportions, including carbon dioxide (CO2), helium, water, nitrogen and hydrogen sulfide (H2S), but also mercury. All of these impurities, especially CO2 and H2S, must be removed from the natural gas stream before transport and commercialization. CO2 and H2S can corrode pipelines, are highly toxic and are significant sources of air pollution. Gases with high levels of H2S and CO2 are also called sour gases.
SBC. October 2014. Factbook Natural Gas Factbook. SBC Energy Institute
- 83% of natural gas comes from conventional reservoirs: 2.9 trillion cubic meters
- 13% of reservoirs account for 70% of global reserves
- The number of discoveries of giant fields has fallen since 1972
- 17% comes from unconventional resources: .6 tcm and 43% of that (2.6 tcm) was produced in the US. In 2013, shale gas accounted for 39% of total natural gas output in the US
- At 3.5 trillion cubic meters (tcm) world-wide production in 2013, reserves will last from Rystad’s 2014 estimate 60.4 tcm for 17 years, or 58 years if OPEC’s estimate of 200 tcm reserves is correct. Page 24
- Technically recoverable resources (the volume of natural gas recoverable with current exploration and production technology and no regard to cost) are 855 tcm and would last 244 years @ 3.5 tcm/year (if we can get them).
- Conventional
- Conventional reservoirs tend to require less technology to be developed and to yield higher recovery rates. However, reservoirs located in deep water or Arctic environments, and those containing a high level of sour gas may also be very challenging to develop.
We are counting on shale gas, but we’re drilling the best “sweet” spots, and even so, it declines rapidly:
Due to the properties of the source rock, shale-gas wells usually exhibit early production peaks and then enter rapid decline – typically 50% over 3 years. In addition, shale-gas plays concentrations of recoverable generally have lower resources – typically around 0.04-0.6 bcm/km2, compared with an average of 2 bcm/km2 in the case of conventional resources. Consequently, shale-gas production requires more wells.
Conventional | Tight Gas | Shale Gas | Coalbed Methane | |
Proved reserves (tcm) | 60.4 | 78.0 | 4.9 | 0.98 |
USA reserves (tcm) | 3.2 | 10.4 | 0.8 | |
Technically recoverable resources (tcm) | 519.0 | 2.3 | 210.0 | 48.0 |
Current Production bcm/y | 2831.0 | 215.0 | 266.0 | 71.0 |
USA Production bcm/y | 211.8 | 133.2 | 242.3 | 52.8 |
Cost of production per Mbtu | $0.2 – 9 (a) | $3 – 9 (b) | $2-10 © | $3-8 (d) |
Recovery Factor % | 60-80 | 30-50 | 8-30 | 50-85 |
Sources:
(a) Source: IEA (2013), “World Energy Outlook 2013”; Rystad databases (accessed May 2014); BP (2013), “BP Statistical World Energy Review 2013”
(b) Rystad databases (accessed May 2014); IEA (2013), “Resources-to-Reserves 2013”; Schlumberger (2011), “Basic Petroleum Geochemistry for Source Rock Evaluation”
(c) Schlumberger (2011), “Shale Gas: A Global Resource”; Schlumberger (2006), “Producing Gas from Its Source”; Rystad databases (accessed May 2014); IEA (2013), “Resources-to-Reserves 2013”
(d) Schlumberger (2009), “Coalbed Methane: Clean Energy for the World”; Rystad databases (accessed May 2014); IEA (2013), “World Energy Outlook”
The slide below is especially scary because it shows that USA conventional reserves are only 26%:
And the United States is producing its reserves at a very rapid rate:
Proved reserves are based on figures from the Organization of the Petroleum Exporting Countries (OPEC) and Rystad (P90 for the latter). They correspond to those quantities of natural gas which, by analysis of geological and engineering data, can be estimated with reasonable certainty to be commercially recoverable, from a given date forward, from known reservoirs and under current economic conditions, operating methods, and government regulations.
Like CO2, methane is a potent greenhouse gas (GHG). However, it has a higher global warming potential (GWP) than CO2. According to the IPCC, methane GWP would be 28 to 84 times higher than CO2 GWP over 100-year and 20-year horizons, respectively.
While abundant, the largest conventional gas resources are concentrated in a small number of countries. In the 2000s, it was thought that Russia, Iran and Qatar owned more than 70% of known conventional gas resources, but recent discoveries of conventional reservoirs in East Africa and the Mediterranean Sea have opened up new gas frontiers, reducing the concentration of natural gas reserves.
According to OPEC, natural gas production was led by North America, Russia, and the Middle East; of this, 83% came from conventional reservoirs.
Raw natural gas collected at the wellhead needs to be processed to meet pipeline quality standards, to ensure safe and clean operations, and to extract valuable natural gas liquids (NGLs). As of 2013, there are close to 2, 000 gas-processing plants operating worldwide, with a global capacity of around 7.6 billion cubic meter (bcm) per day.
About 21% and 10% of all produced natural gas is now traded internationally via, respectively, pipelines and LNG. As a rule of thumb, the longer the shipping distance, the more economically attractive LNG tends to become compared with pipelines. Growth in the LNG trade has been made possible by the expansion of LNG infrastructure: there are now 29 countries with import facilities and 19 with export facilities, trading 237 million tons per annum (Mtpa) of LNG. With new export and regasification facilities under construction, the expansion is expected to continue. Meanwhile, floating liquefaction and regasification concepts have garnered attention as a way of reducing development time, increasing flexibility and lowering capital costs. The first floating storage and regasification units (FSRU) have been commissioned. Four floating liquefaction (FLNG) projects have achieved a final investment decision. Nevertheless, many gas fields are too small or remote to justify pipelines or LNG investment. In order to tap these resources, known as stranded gas, two alternative technologies are being considered: compressed natural gas (CNG) and gas-to-liquids (GTL).
The buildings segment still accounts for 22% of direct natural gas demand and this share is expected to remain stable in the next few decades. Thermal applications are dominant: space heating, water heating and cooking account for 54%, 22% and 11% of natural gas demand in the buildings sector, respectively. The use of natural gas in buildings varies significantly, depending on climate, urbanization patterns, or building design and insulation.
In industry, natural gas is used as a heat source, but also as a chemical feedstock. Direct natural gas consumption represents around 18% of final energy consumption in industry. The chemicals and petrochemicals sectors are by far the most important consumers (accounting for 44% of total industry demand for gas). This is because natural gas is largely used as a source of heat in refineries and as feedstock for producing ammonia and methanol. Other than for chemicals, the bulk of industrial gas demand comes from small-scale industrial consumers using natural gas in small-to medium-scale boilers to generate heat. Any switch from coal to gas in the industrial sector is likely to be relatively limited and subject to the development of carbon pricing.
Conventional gas refers to resources accumulated in a reservoir in which buoyant forces keep hydrocarbons in place below a sealing cap rock. Reservoir and fluid characteristics typically permit natural gas to flow readily into a wellbore. The term unconventional reservoirs, in which gas might throughout a reservoir at the basin scale, and in which buoyant forces are insufficient to expel gas from the reservoir, meaning that intervention is required. Conventional gas reservoirs can either be isolated (non-associated) or associated with oil. Associated gas can be in form of a gas cap (free gas) or it can exist in solution within the oil (solution gas). Natural gas was long considered an unwanted byproduct of oil and was only considered as a commercial prospect when deposits were located close to markets or gas infrastructure.
Coalbed methane is generated during the formation of coal and is contained to varying degrees within all coal microstructure. Because of coal’s porous nature and its many natural cracks and fissures, coal can store more gas than a conventional reservoir of similar volume. However, production from CBM wells can be difficult because of the low permeability of most coal seams. As a result, technologies such as directional drilling and hydraulic fracturing are used to open access to larger areas, enhancing well productivity. Finally, CBM production is often associated with extensive production of water. Water must be removed in order to reduce pressure within the reservoir, making lifting and surface separation more complex and costly. CBM production is advanced in the U.S., Canada and Australia.
Pipelines
Pipelines are the backbone of gas transportation, with a global network of 1. 4 million kilometers
Globally, more than 89% of natural gas is transported along a 1.4 million km pipeline grid. One-third of this network are lines transporting large pressure, large-diameter (6’’-48’’) pipelines. The other two-thirds comprise thinner pipelines at production sites, called gathering lines, and the medium- and low-pressure distribution grids that supply end-customers. Pressure is required to maintain the gas flow. As a result, compression stations are located every 80-160 kilometers along the transport grid. Each station contains one or several compressor units (up to 16). These are classified by their horsepower (up to 50,000-80,000) and gas capacity (up to 90 Mcm/d). Compressors can use a motor (reciprocating) or a turbine (known as centrifugal). Gas-filtering, but also cooling and heating facilities are often included in the station to maintain gas temperature. Gas transport pipelines are usually made of carbon steel and protected against corrosion by external coating and cathodic protection systems.
Pipeline costs vary significantly according to capacity, length and their physical environment, but are dominated by the costs of labor and materials.
Before liquefaction, natural gas must be cleaned to remove contaminants, which might freeze during liquefaction or corrode pipelines. Heavier hydrocarbons are also extracted to meet gas specifications.
LNG
Several liquefaction projects are in development in the U.S., but most are awaiting final investment decisions. Sabine Pass is the only project under construction as of 2014.
Australia is the third largest LNG exporter (22.2 mtpa, or 10% of world exports) after Qatar (77.2 mtpa) and Malaysia (24.7 mtpa) but ahead of Indonesia (17 mtpa). However, Australia, where 53% (63.8 mtpa) of the liquefaction capacity under construction worldwide is located, is expected to take over Qatar as the largest LNG exporter by 2020.
Natural gas prices: for distances up to 9,000 km, LNG tends to require more energy than pipelines, making it more exposed to price increases (i.e. the break-even point between pipeline and LNG may occur over a longer distance than when a pipelines system is used).
Many gas fields are too small or too remote to justify investment in pipelines or LNG facilities. In some environments, the use of pipelines is simply not practical. A possible alternative is compressed natural gas, which is already being used for local gas distribution onshore, but whose application offshore, although conceptually CNG’s main benefit is that it requires relatively little infrastructure, so capital requirements are low : compression is a common feature of most gas-production units and less costly than liquefaction; offloading requires simple buoys. However, CNG has a lower energy density than LNG (typically around one-third, depending on the pressure). As a result, investments in CNG carriers are greater and operating costs are also higher (notably fuel costs).
If the US ever needs to import LNG because shale gas gets too expensive to drill, there are very few regasification plants:
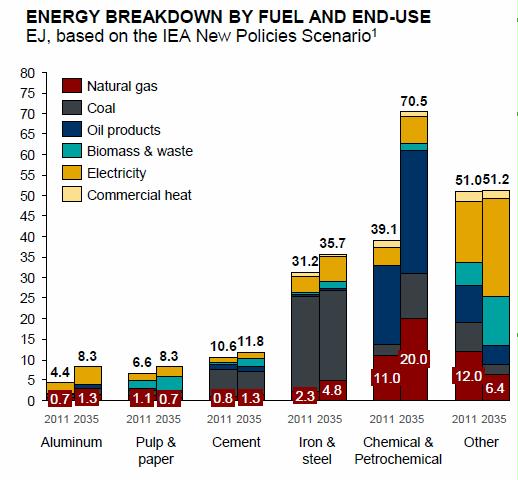
Aluminum, pulp & paper, cement, iron & steel, and chemicals & petrochemicals are the main energy-intensive industries and together account for more than 50% of industrial energy demand
Natural gas plays an important role as a feedstock for producing ammonia, methanol and other hydrocarbon-based products (e.g. olefins, such as ethylene and propylene, using natural gas liquids2). Ammonia is one of the most extensively produced chemicals in the world, helping to create over 500 million tons of nitrogen fertilizer per year. Similarly, methanol is a widespread chemical product, with around 100 million tons used every year as anti-freeze, solvent or fuel. In recent decades, natural gas has become the primary feedstock in ammonia and methanol production. Low natural gas prices and progress in plant design encouraged its use, leading to gains in energy efficiency. Steam methane reforming represents around 77% of hydrogen produced as a basis for ammonia; 75% of methanol production comes from natural gas. In both cases, the remainder is mainly made up of coal
June 2014: The Middle East has 43.2% of the total natural gas deposits in the world (80.3 trillion cu/m) according to the BP Statistical Review of World Energy June 2014 report. Qatar has 24.7 trillion cu/m with Saudi Arabia next in line containing 8.2 trillion cu/m in the region. he International Energy Agency (IEA) has, however, stated that the demand for natural gas will exceed its production from Middle East countries by the year 2019.
25 Jan 2013. Rush to Natural Gas has Coal-fired utilities Seeing Red. Wall Street Journal.
Electricity from Natural Gas is now 30%, up 12% from 10 years ago (18%). From coal: now 37%, down 13% from 10 years ago (50%)
U.S. electricity in trillions of kWh (kilowatt hours):
- Coal 1.7 Trillion
- Natural Gas 1.0 Trillion
- Nuclear .79 Trillion
Some prefer coal power plants, where coal can be stockpiled. Gas is hard to store in bulk near power plants, making plants dependent on natural gas pipelines that simetimes have delivery issues.
Only 3 states buy gas under contracts longer than 3 years (OR, CO, OK).
More than you wanted to know about Natural gas. Below are excerpts. You’d be far better off reading in pdf format where all the pictures and graphs are): SBC. October 2014. Factbook Natural Gas Factbook. SBC Energy Institute. 87 pages
Natural gas is not solely methane. It is composed of a mixture of hydrocarbon components, including methane but also ethane, propane, butane and pentane– commonly known as natural gas liquids (NGLs)– and of impurities such as carbon dioxide (CO2), hydrogen sulfide (H2S), water and nitrogen. The composition is highly variable and depends on the resource’s location. In some fields, contaminants, especially those that characterize sour gas (CO2 or H2S), represent a high proportion of the natural gas mixture, making exploitation harder and more expensive. Sometimes, NGLs – hydrocarbons that are in gaseous form in the reservoir, but that become liquid under ambient conditions– account for a significant share of natural gas; a mix rich in NGLs, known as wet gas. In 2013, wet gas yields 9 million barrels of oil equivalent a day, contributing 10% to global liquid hydrocarbon supply. In all situations, natural gas must be processed to remove NGLs and contaminants.
Natural gas’s main drawbacks relative to other hydrocarbon fuels are its low volumetric energy density and gaseous nature, which makes it harder to handle than solid or liquid fuels. In order to be transported, natural gas needs to be conditioned in some way– either by compression or by liquefaction. This increases shipping costs and results in limited fungibility. The global-warming potential of its main constituent, methane, presents another problem. Similar to CO2, methane is a potent greenhouse gas. However, an equivalent quantity of methane emitted into the atmosphere would entail 84 and 28 more radiative forcings than CO2 over 20- and 100-year horizons, respectively. As a consequence, methane leaks from natural gas systems, if significant and not mitigated, could negate the climate benefit of natural gas compared with other fuels
Natural gas is an energy source that can be used as gaseous fuel, but also in non-gaseous forms– for instance, as electricity after conversion in a turbine or as a liquid after conversion in a gas-to-liquids plant.
Natural gas systems rely on a complex, infrastructure-intensive value chain for extracting, processing, transporting and distributing energy to end customers.
Natural gas resources are usually classified according to the properties of the reservoir in which they are trapped. Resources are referred to as conventional when accumulated in a reservoir whose permeability characteristics permit natural gas to flow readily into a wellbore; and as unconventional when buoyancy forces are insufficient and intervention is required to make the gas flow. Conventional reservoirs are broken down further into, respectively, the non-associated and associated categories, depending on whether gas is found in isolation or dissolved in oil.
There are four main types of unconventional reservoir: tight, shale, coalbed and methane hydrates. Tight and shale accumulations refer to low permeability formations. However, unlike in tight reservoirs, gas in shale rocks has remained in the rock where it formed, making exploration and production more difficult.
Coalbed methane (CBM) is generated during the formation of coal and is contained to varying degrees within all coal microstructure. The presence of this gas is well known from underground coal mining, where it presents a serious safety risk. It is called coal-seam methane in Australia, where it is an important resource. However, producing from CBM wells can be difficult because of the low permeability of most coal seams and the associated production of large volumes of water. In general, unconventional reservoirs tend to yield lower recovery rates than conventional reservoirs, and usually require more technology.
Two technologies have been instrumental in exploiting unconventional resources. Hydraulic fracturing, which involves creating cracks in the rock through which the gas can flow to the wells; and horizontal drilling, which enables wells to penetrate a greater length of the reservoir than is possible with vertical wells, increasing contact with the production zone.
Taken together, natural gas resources are abundant. Depending on data sources and the definition used for reserves, reserves amount to between 69 and 200 trillion cubic meters (tcm) and technically recoverable resources amount to up to 855 tcm. Reserves would, therefore, last between 20 and 58 years, based on a figure for gas consumption in 2013 of 3.5 tcm. Technically recoverable resources, meanwhile, would last over 200 years. While abundant, the largest conventional gas resources are concentrated in a small number of countries. In the 2000s, it was thought that Russia, Iran and Qatar owned more than 70% of known conventional gas resources.
Unconventional resources are much more widespread and recent discoveries of conventional reservoirs in East Africa or the Mediterranean Sea have opened up new gas frontiers, reducing the concentration of natural gas reserves.
According to the OPEC, natural gas production reached 3.5 tcm in 2013, led by North America, Russia, and the Middle East; of this, 83% came from conventional reservoirs. However, while conventional reservoirs continue to dominate production, output from unconventional accumulations grew 9 times faster than conventional production in 2013, reaching 0.6 tcm. Production from shale reservoirs in the U.S. has been the main driver of growth and now represents 43% of global unconventional gas production. Going forward, natural gas production is expected to continue to increase, driven by unconventional resources and new conventional resources (associated and non-associated gas). For instance, Rystad forecasts that natural gas production will reach 4.6 tcm by 2035.
Complex infrastructure is needed to get natural gas to end-users – processing plants, transport & distribution grids, and storage units
Raw natural gas collected at the wellhead needs to be processed to meet pipeline quality standards, to ensure safe and clean operations, and to extract valuable natural gas liquids (NGLs). As of 2013, there are close to 2, 000 gas-processing plants operating worldwide, with a global capacity of around 7.6 billion cubic meter (bcm) per day. More than half of capacity is located in North America, but the Middle East and Asia, where utilization rates (i.e. gas processing throughput / gas-processing capacity) are much higher than in the U.S., are expected to take over as market drivers.
The low energy density of natural gas has long been an impediment to long- distance transportation, and most natural gas is still consumed close to production centers. However, long-distance trade has increased steadily in recent decades. Along with pipelines, which have been in use since the 19th century, LNG is playing a growing role in long-distance shipping. About 21% and 10% of all produced natural gas is now traded internationally via, respectively, pipelines and LNG. As a rule of thumb, the longer the shipping distance, the more economically attractive LNG tends to become compared with pipelines. Growth in the LNG trade has been made possible by the expansion of LNG infrastructure: there are now 29 countries with import facilities and 19 with export facilities, trading 237 million tons per annum (Mtpa) of LNG. With new export and regasification facilities under construction, the expansion is expected to continue. Meanwhile, floating liquefaction and regasification concepts have garnered attention as a way of reducing development time, increasing flexibility and lowering capital costs. The first floating storage and regasification units (FSRU) have been commissioned. Four floating liquefaction (FLNG) projects have achieved a final investment decision. Nevertheless, many gas fields are too small or remote to justify pipelines or LNG investment. In order to tap these resources, known as stranded gas, two alternative technologies are being considered: compressed natural gas (CNG) and gas-to-liquids (GTL).
The former is already in use onshore, but its application offshore is still at an early deployment phase. The latter is technically mature but still in its commercial infancy, with only four plants operating worldwide and subject to the development of economically viable small-scale modular systems.
Underground storage vessels include depleted oil and gas fields, aquifers and salt formations; the choice depends on local geology and how the storage facility will be used. Flexibility in storage capacity has become an important parameter because of growth in the use of natural gas in power generation and because of the limited flexibility of production from unconventional gas reservoirs. As a result, salt caverns have become popular; although they are relatively expensive, their flexibility is unrivalled.
natural gas needs to be pressurized, odorized and controlled to be safely delivered to end-customers. Except for a few large customers, most end- users are supplied through low-pressure networks.
Local distribution involves smaller delivery volumes than long-distance transmission, and delivery over shorter distances to many more locations. As a consequence, distribution lines make up the majority of installed pipelines. Ensuring safety is the main challenge faced by distribution-grid operators.
natural gas plays a major role in all end-use sectors, except for transport. Power generation is the main driver of natural gas consumption, representing 40% of gas demand globally, up from 35% in 1990.
For many years, the use of natural gas in commercial and residential buildings was the backbone of natural gas demand. The buildings segment still accounts for 22% of direct natural gas demand and this share is expected to remain stable in the next few decades. Thermal applications are dominant: space heating, water heating and cooking account for 54%, 22% and 11% of natural gas demand in the buildings sector, respectively. The use of natural gas in buildings varies significantly, depending on climate, urbanization patterns, or building design and insulation.
In industry, natural gas is used as a heat source, but also as a chemical feedstock. Direct natural gas consumption represents around 18% of final energy consumption in industry. The chemicals and petrochemicals sectors are by far the most important consumers (accounting for 44% of total industry demand for gas). This is because natural gas is largely used as a source of heat in refineries and as feedstock for producing ammonia and methanol. Other than for chemicals, the bulk of industrial gas demand comes from small-scale industrial consumers using natural gas in small-to medium-scale boilers to generate heat. Any switch from coal to gas in the industrial sector is likely to be relatively limited and subject to the development of carbon pricing.
1785 First commercial use of manufactured gas1 fuel for lighting.
1812 First gas company founded in London.
1885 Bunsen burner invented: ability to create a flame safe enough for cooking and heating applications 1936 First industrial gas turbine developed independently from jet engine.
1970s First combined-cycle power plants with a power output around 200 MW.
2000s Major development programs for compressed natural gas vehicles 1800 1850 1900 1950 2000 MANUFACTURED GAS CONVENTIONAL GAS & UNCONVENTIONAL GAS 1785 1821 First well specifically intended to obtain natural gas drilled in Fredonia, New York. 1872 First long-distance natural gas pipeline in the U. S. completed in Pennsylvania. 1915 1947 Hydraulic fracturing first used in U.S. 1951 First production of natural gas from coal beds. 2014 1995 Hydraulic fracturing and horizontal drilling led to successful exploitation of shale gas in Barnett, Texas. 1959 First use of depleted reservoirs for natural gas Methane Pioneer shipped the first cargo of LNG from storage. the U.S. to the U.K. 1992 World’s largest gas field, South Pars/North Field fully delineated. Note: 1Manufactured
Organic matter, such as the remains of recently living organisms ( e.g. plants, algae, animals, plankton…), is the origin of all the hydrocarbons generated in the earth. A very small portion of this organic matter is deposited in poorly oxygenated aqueous environments (seas, deltas, lakes…), where it is protected from the action of aerobic bacteria and is mixed with sediments to form the source rock.
Over time, the weight of gradually accumulating organic material and debris causes source rock to subside to great depths, where its organic content entrapped in a mud-like substance known as kerogen, is subject to increasing temperature and pressure.
These conditions lead to the thermal cracking of kerogen’s long molecular chains into smaller and lighter hydrocarbon molecules1. During the catagenis phase (50-150°C), kerogen bounds are gradually cracked into oil or into wet gas depending on the kerogen type. As temperatures rise in proportion with depth, hydrocarbon molecules become lighter as depth beneath the surface increases. During a last stage, known as metagenesis, additional heat and chemical changes eventually convert most of the remaining kerogen into methane and carbon residues. Hydrocarbon molecules are then expelled from the source rock during a “primary migration” phase, mainly as a consequence of high pressures. Hydrocarbons will then set off on a“secondary migration phase, making their way upward through rocky layers. If stopped by an impermeable layer of rock, also referred to as seal, hydrocarbons may accumulate in the pores and fissures of a reservoir rock. Otherwise, they may escape from the surface or solidify into bitumen.
Methane [CH4] is the chief constituent of most natural gas, but it may also contain lesser amounts of ethane [C2H6], propane [C3H8], butane [C4H10] and pentane [C5H12], commonly known as natural gas liquids (NGLs).
Impurities can also be present in large proportions, including carbon dioxide (CO2), helium, water, nitrogen and hydrogen sulfide (H2S), but also mercury. All of these impurities, especially CO2 and H2S, must be removed from the natural gas stream before transport and commercialization. CO2 and H2S can corrode pipelines, are highly toxic and are significant sources of air pollution. Gases with high levels of H2S and CO2 are also called sour gases.
Components heavier than methane, known as natural gas liquids (NGLs), represent 10% of global liquid hydrocarbon supply
Hydrocarbon components of natural gas that are heavier than methane are called natural gas liquids (NGLs). They can be extracted in a processing plant2 and commercialized as liquid fuels. Natural gas that is rich in NGLs is usually called wet gas or rich gas, as opposed to dry gas or lean gas. Liquefied petroleum gas (LPG), to make a further distinction, is a subset of NGLs, comprising propane and butane. LPG can be liquefied through pressurization (i.e. without requiring cryogenic refrigeration), and used as a liquid fuel.
In 2012, supply of NGLs amounted to 9 million barrels a day, representing about 10% of world liquid hydrocarbon production. While total liquid supply has increased at a 1% compound average annual growth rate (CAGR) since 1980, NGLs production has more than doubled with a CAGR of 3.1%.
In some fields, contaminants can be found in very high concentrations. This increases investment needs and production costs to the extent that production may even be rendered uneconomic. Natural gas rich in hydrogen sulfide (H2S) or carbon dioxide (CO2) is called sour gas or acid gas. CO2 and H2S are both extremely corrosive and H2S is also toxic. When these gases are present, special equipment is needed (e.g. special alloys for tubing and piping) to ensure that the natural gas can be safely transported and processed, prior to being sold.
20-40% of global recoverable gas resources could be considered, to varying degrees, to be sour gas, especially in the Middle East and Central Asia, but also in North America, Australia and Russia. Even if sour gas fields have a long history of successful development in several places, lowering the costs of sour-gas operation is essential if its potential is to be fully tapped. This could be through innovation in gas-separation technologies used in processing plants or more advanced deployment of capture and re-injection, including enhanced oil recovery.
Natural gas’s volatility and low energy density make handling it difficult
VOLUMETRIC ENERGY DENSITY OF CHEMICAL FUELS1 ? Natural gas’s main drawback relative to other MJ/liter hydrocarbon fuels is its low volumetric energy density, i.e. energy stored per unit of volume. This becomes especially challenging when natural gas is used as a Diesel transport fuel. In addition, its gaseous nature makes it volatile and harder to handle than solid fuels like coal or Gasoline liquid fuels such as crude oil.35 ? As a consequence, natural gas needs to be“packaged” in some way in order to increase its energy density and to allow for safe and economic transport and storage. Two main conditioning technologies are used: 1) compression, in which natural gas is pressurized, and 2
liquefaction, in which cryogenic refrigeration turns natural gas into a liquid. Compression is by far the most common handling technology, but liquefaction, which results in Liquefied natural gas 22 greater energy density, is also a mature technology and common in long-distance transport2. Finally, natural gas can Methanol also be converted into liquid fuels in a process known as gas-to-liquids (GTL)3.
Whatever the technology, gas conditioning incurs high handling costs and has limited flexibility. Unlike oil, for instance, which is fungible, natural gas relies on a heavy infrastructure pressurized or storage caverns or cryogenic carrier).
Without such infrastructure, natural gas would be flared or vented
Like CO2, methane is a potent greenhouse gas (GHG). However, it has a higher global warming potential (GWP) than CO2. According to the IPCC, methane GWP would be 28 to 84 times higher than CO2 GWP over 100-year and 20-year horizons, respectively.
Conventional reservoirs tend to require less technology to be developed and to yield higher recovery rates. However, reservoirs located in deep water or Arctic environments, and those containing a high level of sour gas may also be very challenging to develop.
Conventional gas refers to resources accumulated in a reservoir in which buoyant forces keep hydrocarbons in place below a sealing cap rock. Reservoir and fluid characteristics typically permit natural gas to flow readily into a wellbore. The term unconventional reservoirs, in which gas might throughout a reservoir at the basin scale, and in which buoyant forces are insufficient to expel gas from the reservoir, meaning that intervention is required. Conventional gas reservoirs can either be isolated (non-associated) or associated with oil. Associated gas can be in form of a gas cap (free gas) or it can exist in solution within the oil (solution gas). Natural gas was long considered an unwanted byproduct of oil and was only considered as a commercial prospect when deposits were located close to markets or gas infrastructure.
Coalbed methane is generated during the formation of coal and is contained to varying degrees within all coal microstructure. Because of coal’s porous nature and its many natural cracks and fissures, coal can store more gas than a conventional reservoir of similar volume. However, production from CBM wells can be difficult because of the low permeability of most coal seams. As a result, technologies such as directional drilling and hydraulic fracturing are used to open access to larger areas, enhancing well productivity. Finally, CBM production is often associated with extensive production of water. Water must be removed in order to reduce pressure within the reservoir, making lifting and surface separation more complex and costly. CBM production is advanced in the U.S., Canada and Australia.
Methane hydrates could considerably increase natural gas resources but are still at a very early development phase Four production methods are under investigation for methane-hydrate recovery: 1) depressurization, which has emerged as the preferred solution, involves lowering the water level in the well; 2) thermal stimulation, which involves warming the formation; 3) chemical inhibition, which exploits the ability of certain organic or ionic compounds to destabilize gas hydrates; and 4) CO2 injection.
The industry does not expect any large-scale commercial production to happen before 2030 because of the considerable technology and environmental barriers faced. Besides, the development of methane hydrates has been affected by the shale-gas revolution. The latter has resulted in new– and less concentrated– gas resources, and in lower gas prices in most regions.
Conventional reserves in Russia and the Middle East, and unconventionals in North America make the largest contributions to natural gas reserves
Natural gas resources are relatively concentrated geographically: 13% of discovered reservoirs account for 70% of global reserves
Giant gas fields– with recoverable totals that exceed 100 bcm– hold more than 70% of global reserves but account for just 13% of the total number of fields.
The number of fields discovered each year increased steadily between 1950 and 1982, and has remained high ever since. But growth in the size of discoveries slowed down after 1972 as the number of giant discoveries fell.
Resources in unconventional reservoirs are expected to account for an increasing share of natural gas production
According to natural gas continue to increase, albeit at a slower pace, reaching 4.6 tcm/y by 2035. Shale reservoirs would make the single-largest contribution accounting incremental 2035, unconventional gas production could account for 27% of the natural gas mix2. Nevertheless, forward- looking projections of this type are sensitive to numerous parameters, such as advances in technology, global or regional economic growth, policies and incentives, and the availability alternative should remember that, just 10 years ago, a supply shortage was widely predicted for North America.
In 2013, shale gas accounted for 39% of total natural gas output in the U. S., the leading producer, with 90% of global shale-gas supply U.S.
Between 2007 and 2012, natural gas production from shale in the United States more than quadrupled3.
Natural gas production profiles in conventional formations vary significantly, according to field size, location and management. Larger fields are generally characterized by longer production plateaus than smaller fields. Offshore reserves are recovered more quickly than onshore ones: offshore production increases more rapidly and settles at a higher plateau. One-third of reserves are generally produced during the plateau.
Due to the properties of the source rock, shale-gas wells usually exhibit early production peaks and then enter rapid decline – typically 50% over 3 years. In addition, shale-gas plays concentrations of recoverable generally have lower resources – typically around 0.04-0.6 bcm/km2, compared with an average of 2 bcm/km2 in the case of conventional resources. Consequently, shale-gas production requires more wells.
The ramp-up of CBM production is slower than the ramp-up of conventional and shale-gas production. This is because of the large quantity of water, naturally occurring or introduced during fracking, that must be extracted in order to reduce pressure within the formation sufficiently to allow gas to flow to the wellbore. Natural gas production then increases as the volume of water produced decreases.
Complex infrastructure is needed to get natural gas to end-users – processing plants, transport & distribution grids, and storage units
Processing is an essential step in turning raw natural gas into a commercial product and extracting natural gas liquids (NGLs)
Natural gas collected at the wellhead must usually be processed to meet the pipeline-quality standards defined by each system (energy content, water content…) and to ensure safe and clean operation, both of the grid and of end-appliances. The type of gas processing required depends on the composition of the raw gas and on the pipeline system’s quality specifications. Although it is less complex than crude-oil refining, natural-gas processing is a crucial stage in the natural gas value chain. In addition to its primary purpose, cleaning,
Gas-processing plants are located all over the world, since they are usually sited close to production centers. However, it is worth noting that, as of 2013, 50% of processing capacity was concentrated in North America, which accounts for only 24.9% of world production. Iran, Algeria and Indonesia have processing capacities that correspond to their respective shares of production.
As of 2013, there were 1,954 gas-processing plants operating in the world, with a global capacity of 7,657 mcm/d. In 2012, these plants operated at an average utilization rate of 57%, processing a throughput of natural gas of 4. 432 mcm/d.
Despite the emergence of significant global LNG flows, gas trade remains dominated by regional pipeline trade
MAJOR TRADE MOVEMENTS BY PIPELINE (2012) AND LNG
Pipelines are the backbone of gas transportation, with a global network of 1. 4 million kilometers
Globally, more than 89% of natural gas is transported along a 1.4 million km pipeline grid. One-third of this network are lines transporting large pressure, large-diameter (6’’-48’’) pipelines. The other two-thirds comprise thinner pipelines at production sites, called gathering lines, and the medium- and low-pressure distribution grids that supply end-customers. Pressure is required to maintain the gas flow. As a result, compression stations are located every 80-160 kilometers along the transport grid. Each station contains one or several compressor units (up to 16). These are classified by their horsepower (up to 50,000-80,000) and gas capacity (up to 90 Mcm/d). Compressors can use a motor (reciprocating) or a turbine (known as centrifugal). Gas-filtering, but also cooling and heating facilities are often included in the station to maintain gas temperature. Gas transport pipelines are usually made of carbon steel and protected against corrosion by external coating and cathodic protection systems.
North America, TransCanada Alaska will connect Alaska to Alberta and the U. S., while an 804 km pipeline is planned from Arizona to the northwest of Mexico.
Pipeline costs vary significantly according to capacity, length and their physical environment, but are dominated by the costs of labor and materials.
Before liquefaction, natural gas must be cleaned to remove contaminants, which might freeze during liquefaction or corrode pipelines. Heavier hydrocarbons are also extracted to meet gas specifications.
Vessel design is dictated largely by the high energy density and extremely low temperature of LNG. LNG carriers must be double-hulled, with water ballast. On-board storage tanks require special alloys to ensure effective insulation.
Several liquefaction projects are in development in the U.S., but most are awaiting final investment decisions. Sabine Pass is the only project under construction as of 2014.
Australia is the third largest LNG exporter (22.2 mtpa, or 10% of world exports) after Qatar (77.2 mtpa) and Malaysia (24.7 mtpa) but ahead of Indonesia (17 mtpa). However, Australia, where 53% (63.8 mtpa) of the liquefaction capacity under construction worldwide is located, is expected to take over Qatar as the largest LNG exporter by 2020.
Natural gas prices: for distances up to 9,000 km, LNG tends to require more energy than pipelines, making it more exposed to price increases (i.e. the break-even point between pipeline and LNG may occur over a longer distance than when a pipelines system is used).
Many gas fields are too small or too remote to justify investment in pipelines or LNG facilities. In some environments, the use of pipelines is simply not practical. A possible alternative is compressed natural gas, which is already being used for local gas distribution onshore, but whose application offshore, although conceptually CNG’s main benefit is that it requires relatively little infrastructure, so capital requirements are low : compression is a common feature of most gas-production units and less costly than liquefaction; offloading requires simple buoys. However, CNG has a lower energy density than LNG (typically around one-third, depending on the pressure). As a result, investments in CNG carriers are greater and operating costs are also higher (notably fuel costs).
Small-scale gas-to-liquid (GTL) conversion systems may provide an alternative means of transporting and monetizing stranded gas
Despite its discovery in the early 20th Century, and past use on a relatively large scale by Germany and South Africa, the gas-to-liquids (GTL) process is still in its commercial infancy. As of 2013, there were four commercial GTL plants operating worldwide. The largest, Shell’s Pearl GTL, started operation in 2010 in Qatar, with a capacity of 140,000 bbl/day.
Concerns have lead to project cancellations (Shell in Louisiana andTalisman’s exit from Montney in Canada). Pearl’s costs were estimated to have tripled compared with its initial budget, rising to $18-19 bn. Despite a favorable price spread between oil and gas, capital costs are still too high (e.g. $80,000 per bbl/d of capacity for Pearl) and energy efficiency too low (as a rule-of-thumb, only a tenth of the energy in natural gas used in the GTL process is converted into useable products) to justify GTL on large-scale.
Small-scale, modular GTL systems seem to be the key to GTL becoming more widespread. These would have the ability to monetize stranded gas and associated gas resources that are currently flared, notably those offshore. Small-scale GTL also obviates the construction of an on-site reforming unit, reducing capital costs1. As a general estimate, if 50% of the gas that is flared were to be used as GTL feedstock, it would produce around 7 mbbl/d of additional liquid fuels. R,D&D efforts (catalyst…) remain crucial in reducing costs and improving efficiency.
Aquifers are porous, permeable, underground rock formations that act as natural water reservoirs and can be used to store gas when overlaid by an +impermeable cap rock. However, aquifers require more cushion gas1 (50-80%) than depleted fields and more investment in injection infrastructure. They are +usually, therefore, utilized only when there are no depleted fields nearby. They usually have high delivery rates and are used for balancing seasonal variations (summer/winter) in supply and demand.
Salt formations, whether bedded salt or salt domes, can be used to store gas due tosalt’s natural insulation properties. They are usually more expensive + than the alternatives, since– unless abandoned mines are used– a cavern has to be created. However, they require a small proportion of cushion gas1 +
However, recently, natural gas storage needs have radically evolved, as natural gas trade has become more liquid and as natural gas’s role in power generation has grown: Storage provides a means of hedging against natural gas price volatility, especially in the most liquid markets, North America and Western Europe; Storage requirements are also affected by natural gas’s increasing share of power generation. Indeed, many countries now use open-cycle gas turbines in peaker mode to balance supply from intermittent renewables. This variability from the procurement. transfers unpredictability and power sector into natural gas In both cases, the flexibility of storage capacity has become essential, generating new momentum behind salt caverns, which provide unrivalled flexibility, albeit at a high cost.
Natural gas needs to be depressurized, odorized and monitored to be safely delivered to end-customers through a dense network of small pipelines for a few customers, such as power stations or large industrial plants, which are connected directly to the high-pressure transmission system (up to 75 bar), most end-customers are supplied by the low-pressure gas network (up to 1 bar, and ~20 mbar at the meter)2. Unlike long-distance transportation, distribution is characterized by smaller volumes transported to many more locations, over shorter distances. As a consequence, distribution accounts for most of the pipelines installed
Historically, natural gas has played a crucial role in increasing oil- recovery rates
Oil’s natural flow results in low primary recovery factors, typically 5- 15%2. Various techniques are therefore used to improved recovery rates. These include a number of artificial-lift techniques. One of the most common, especially in mature offshore wells, involves injecting natural gas through the tubing-casing annulus in a producing oil well. Injected gas creates bubbles in the produced fluid, making the liquid less dense and allowing pressure in the formation to lift the column of fluid3.
New techniques have been developed to cope with more complex offshore environments (e.g. new valves or auto-gas lift to meet the safety and pressure requirements of deepwater oil fields). Natural gas can also be injected to maintain sufficient pressure in reservoirs. Also known as gas flooding, this involves “pushing” oil towards the wellbore. Natural gas injection, usually into the gas cap, is the preferred method of disposing of or storing associated gas when it has no economic value or to balance continuous supply rate with seasonal variations in demand. Gas can be injected as part of enhanced recovery. This differs from gas flooding because it changes the make-up of the reservoir. Various gases can be injected: natural gas, produced from the same or a neighboring field, exhaust gas from a nearby industrial plant/power plant, nitrogen, once separated, and carbon dioxide. The latter is the most popular and serves at the same time as a means of sequestering anthropogenic sources of a greenhouse gas.
Natural gas’s role in the global energy mix is growing
Natural gas demand is currently divided among three main generation; residential buildings; and industry. The power sector is fastest-growing driver demand (40%). Electricity is followed by industry (23%), where natural gas can be used as fuel or as a chemical feedstock, and by demand from commercial and residential buildings (22%). Transport is the only end-use sector in which natural gas does not yet play a central role.
Gas power-generation technologies are attractive because of their considerable flexibility and high degree of efficiency
There are two dominant gas power generation technologies: open-cycle gas turbine (OCGT) and combined cycle gas turbine (CCGT). Both are based on the same principle: compressed air is ignited by natural gas combustion. This spins a turbine, whose high-speed rotations drive an electric generator. However, unlike OCGT, CCGT makes use of waste heat from the gas turbine:
exhaust gas is captured to boil water into steam in order to feed an additional turbine. CCGT has contributed 73% of gas-turbine capacity additions since 1990.CCGT’s efficiency and relatively low capital costs– combined with its high degree of flexibility and economic competitiveness with coal, even when utilization rates are high– have strongly influenced growth in the use of natural gas in power generation. However, for peaking uses, which require a very high degree of flexibility, OCCT is still favored.
Natural gas power plants tend to be an important source of flexibility for power systems because of the flexibility of natural gas turbines. System operators use gas-fired power plants to match supply and demand by adjusting their output upwards or downwards1. As a consequence, natural gas power plants are typically operated as mid-merit plants (i.e. running ~50% of the time) or peaking plants (i.e. running less than 20% of the time), as opposed to baseload plants, such as nuclear or coal units, which are used virtually all year-long to leverage their relatively low operating costs and amortize their relatively high initial investment.
Overall, buildings represent 22% of the world’s direct natural gas demand. When natural gas used to generate electricity and commercial heat for buildings is added, the share rises to almost 29%. The direct use of natural gas in buildings is predominantly for thermal end-uses. Space and water heating represent 54% and 22% of natural gas use in buildings, respectively, and heat for cooking 11%. Within buildings, the commercial sector represents 30% of total gas consumption and the residential sector 70%.
The chemicals and petrochemicals sector is by far the most important consumer of natural gas in industry (44% of all industrial demand). In this industry, natural gas is not only used as a fuel, but also as a feedstock for producing ammonia, methanol and other chemicals. In other energy intensive industries2, natural gas continues to play a secondary role e.g. in the iron & steel sector, coal accounts for 74% of the energy mix, compared with 7% in the case of natural gas). Therefore, with the exception of the chemicals & petrochemicals industry, the bulk of industrial gas demand comes from a wide range of industrial consumers who use natural gas in small-to-medium-scale boilers to generate heat.
Natural gas is a crucial feedstock for the petrochemicals and fertilizer industries
Natural gas plays an important role as a feedstock for producing ammonia, methanol and other hydrocarbon-based products (e.g. olefins, such as ethylene and propylene, using natural gas liquids2). Ammonia is one of the most extensively produced chemicals in the world, helping to create over 500 million tons of nitrogen fertilizer per year. Similarly, methanol is a widespread chemical product, with around 100 million tons used every year as anti-freeze, solvent or fuel. In recent decades, natural gas has become the primary feedstock in ammonia and methanol production. Low natural gas prices and progress in plant design encouraged its use, leading to gains in energy efficiency. Steam methane reforming represents around 77% of hydrogen produced as a basis for ammonia; 75% of methanol production comes from natural gas. In both cases, the remainder is mainly made up of coal
CNG refueling stations require lower investment costs than LNG refueling stations and result in lower GHG emissions (because CNG processes are less energy intensive). It would also be easier to refit vehicles to run on CNG or as bi-fuel vehicles.
The liquefaction process also incurs an energy penalty and regular vehicle use is required to minimize fuel losses arising from boil-off.
Conversion is costly and incurs significant energy losses (especially for drop-in gasolines and diesels, which could be used without modification to the existing system).
natural-gas vehicles have a poorer range and their fuels require expensive conditioning. Finally, the impact on global warming of using natural gas for powering vehicles remains uncertain and highly system-specific. Indeed, well-to-wheel analysis depends heavily on whether or not there is methane leakage at any stage in the process (see slide 17).