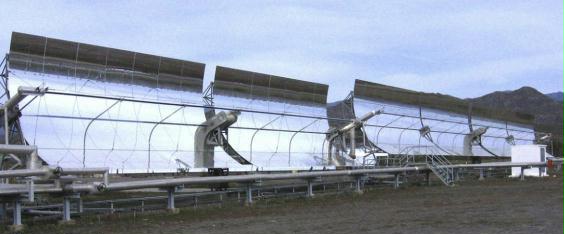
Preface. The bright future of solar thermal powered factories, makes some important points about using concentrated solar power to generate heat:
“…A large share of energy consumed worldwide is by heat. Cooking, space heating and water heating dominate domestic energy consumption. In the UK, these activities account for 85% of domestic energy use, in Europe for 89% and in the USA for 61%. Heat also dominates industrial energy consumption. In the UK, 76% of industrial energy consumption is heat. In Europe, this is 67%. Few things can be manufactured without heat.
Although it is perfectly possible to convert electricity into heat, as in electric heaters or electric cookers, it is very inefficient to do so. It is often assumed that our energy problems are solved when renewables reach ‘grid parity’ – the point at which they can generate electricity for the same price as fossil fuels. But to truly compete with fossil fuels, renewables must also reach ‘thermal parity‘.
It still remains significantly cheaper to produce heat with oil, gas or coal than with a wind turbine or a solar panel.
In today’s solar thermal plants, solar energy is converted into steam (via a steam boiler), which is then converted into electricity (via a steam turbine that drives an electric generator). This process is just as inefficient as converting electricity into heat: two-thirds of energy gets lost when converted from steam to electricity. If we were to use solar thermal plants to generate heat instead of converting this heat into electricity, the technology could deliver energy 3 times cheaper than it does today.
43% of industrial heat demand in Europe is above 400 °C (752 °F). These include many of the industrial processes that we need to manufacture renewable energy sources (wind turbines, solar panels, flat plate collectors and solar concentrators) as well as other green technologies (like LEDs, batteries and bicycles). Examples include the production of glass (requiring temperatures up to 1,575 °C/2870 F) and cement (1,450 °C / 2640 F), the recycling of aluminum (660 °C / 1220 F) and steel (1,520 °C / 2770 F), the production of steel (1,800 °C / 3275 F) and aluminum (2,000 °C / 3600 F) from mined ores, the firing of ceramics (1,000 to 1,400 °C / 1830 to 2550 F) and the manufacturing of silicon microchips and solar cells (1,900°C / 3450 F )“.
Matt Egan (2019) has an article on CNN titled “Secretive energy startup backed by Bill Gates achieves solar breakthrough“. This big breakthrough will allow a solar oven to generate 1000 C (1800 F). As you can see from the above industrial products that’s not nearly enough.
These concentrated solar power contraptions can only be constructed in areas with almost no water in the atmosphere, mainly the desert Southwest in the U.S.
Heat can’t travel far. it’s too hard to transfer hot fluids like steam more than a few hundred meters, while electricity can be sent for hundreds of miles. So solar collectors need to be next to the manufacturing plant.
The CSP in Egan’s article uses mirrors to concentrate sunlight into a very small area. That means Ford, DuPont, U.S. Steel and all other industries that need cement or metal will need to move to the Southwest right next to the CSP plant (so far, CSP plants have cost about $1 billion each) and fight over which piece of a companies product can be made in the tiny area where the solar rays are concentrated during the brief 10 am to 2 pm window when high heat can be generated.
Oh, you say. Each company can build their own $1 billion CSP plant. That won’t be easy. Siting a CSP plant is difficult, because most of the suitable land is federal, and it can take quite a long time to get permission to build on protected federal land. It’s also hard to get permits for water in these dry regions, since cities and agriculture are usually considered to be more important and CSP competes with agriculture for level land with less than a 1% slope. CSP locations are far from rivers and lakes, making groundwater the only possible source of water. In Arizona, it is hard to get permission to obtain groundwater without a grandfathered water right on that land or get a special permit in many regions.
Let’s hope industries don’t need water for anything! Current estimates indicate that operational CSP plants use at least 620 acre-feet per year. That’s 765,000 cubic meters of water, 202 million gallons in the desert regions of the Southwest (Arizona, California, and Nevada). CSP facilities with wet cooling can consume more water per unit of electricity generated than traditional fossil fuel facilities using wet cooling.
Alice Friedemann www.energyskeptic.com author of “When Trucks Stop Running: Energy and the Future of Transportation”, 2015, Springer and “Crunch! Whole Grain Artisan Chips and Crackers”. Podcasts: Derrick Jensen, Practical Prepping, KunstlerCast 253, KunstlerCast278, Peak Prosperity , XX2 report
***
Kurup, P., et al. 2015. Initial Investigation into the Potential of CSP Industrial Process Heat for the Southwest United States. National Renewable Energy Laboratory.
Alice Friedemann www.energyskeptic.com author of “When Trucks Stop Running: Energy and the Future of Transportation”, 2015, Springer and “Crunch! Whole Grain Artisan Chips and Crackers”. Podcasts: Practical Prepping, KunstlerCast 253, KunstlerCast278, Peak Prosperity , XX2 report
***
Industries use enormous amounts of fossil fuels to generate heat and electricity to make products like steel, cement, chemicals, glass, and refine petroleum, with nearly three-quarters of energy used in the form of heat. Industry uses 30% of all energy, and 83% of that energy is generated by fossil fuels mainly to create process heat directly, indirectly with steam heat, or to generate electricity at the factory for reliability and to operate machine drive equipment (EI 2010).
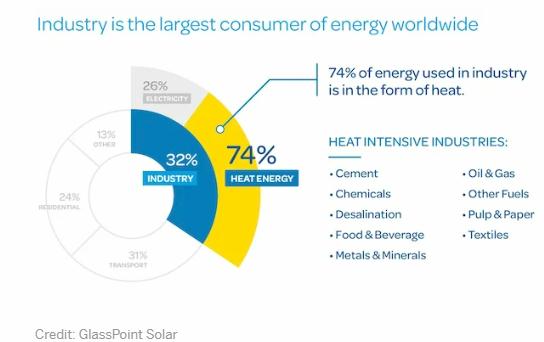
It is possible for a Parabolic Trough collector (PTC), which looks like a giant upended cattle trough, to make some of this industrial heat and replace some of the fossil fuels used (mainly natural gas).
But the industrial uses this concentrated solar power collection is most useful for are heat applications from 110 to 220 C (230 – 430 F), especially those processes that use pressurized water or steam.
So that leaves quite a few very important industries out, since they use 2000 F heat or more, such as iron, steel, fabricated metals, transportation equipment (cars, trucks), computers, electronics, aluminum, cement, glass, machinery, and foundries.
Industries where solar industrial process heat (SIPH) might be used are paper, dairy, food, beer, chemicals, and washing/cleaning. No doubt some processes within other industries like plastics and rubber, textiles, and others also have a need for industrial process heat that’s less than 430 F.
NREL isn’t proposing gigantic, billion dollar concentrated solar power collectors like the ones that take up miles of land in the deserts of California, Nevada, and Arizona.
Rather they suggest that much smaller facilities could be built. Have been built actually, Frito Lay set aside 5 acres to use heat to fry potato chips in Modesto, California. Prestage Foods in North Carolina also has 7 acres of PTC to heat 100,000 gallons of water a day for their turkey processing operations. Currently there are 16 other SIPH plants (9 food & dairy, 4 breweries, 2 desalination & water treatment, 1 subway washing).
Another reason these plants need to be small and local is that unlike electricity, it’s too hard to transfer hot fluids like steam more than a few hundred meters, while electricity can be sent for hundreds of miles. So solar collectors need to be next to the manufacturing plant.
But SIPH can barely make a dent in the industrial process heat required. In 2013 a German study found that solar heat generation could only replace 3.4% of overall industrial heat demands. This 3.4% would require 16 Terawatt hours (TWh) a year, which would require 46 Nevada Solar One plants. This plant cost $266 million, so that’s $12.2 billion for this small fraction of manufacturing.
Like all electricity generating contraptions, PTC and other concentrated solar power collectors can’t outlast the age of oil, since their life cycle depends on fossil fuels from beginning to end — from mining, ore crushing, metal smelting and fabrication, transportation by diesel trucks, ships, and trains, and finally delivery with een more diesel. If solar collectors were good at generating the 3000 F temperatures needed by iron, steel, and aluminum, or the 2700 F needed by cement these contraptions, then they’d come closer than wind or solar PV towards replacing fossils and being able to make themselves from their own energy, but that simply isn’t the case.
Just look at the materials needed for a 1 Gigawatt Parabolic trough collector:
High heat
Material Tons > PTC can generate
Water 12,000,000
Rock 1,300,000
Iron 650,000 Yes
NaNO3 340,000
Cement 250,000 Yes
Steel 240,000 Yes
Sodium Nitrate 220,000
Limestone 170,000
Glass 130,000 Yes
Silicon sand 92,000
Table 1. Materials needed per GW for a parabolic trough collector (Pihl 2012)
In addition thousands of tons of Copper (3200), Chromium (2200), Foam glass (2500), Magnesium (3000), Manganese (2000), Rock Wool (4700), Soda Ash (18,000), and hundreds of tons of Aluminum (740), Fibreglass (310), Molybdenum (200), Polypropylene (500), Zinc (650) and many more materials as well.
The years of reserve life for many aren’t far off Iron (33), Copper (39), Manganese (48), Chromium (16), Nickel (49), Molybdenum (43), Niobium (48), and Silver (25), so solar collector contraptions, if not limited by oil, natural gas, and coal for their construction will be limited by their materials.
References
EI. 2010. Manufacturing Energy and Carbon Footprint Sector: All Manufacturing (NAICS 31-33). Energetics Incorporated for the U. S. Department of Energy
Pihl, E., et al. 2012. Material constraings for concentrating solar thermal power.
Related posts:
- Concentrated Solar Power: Water Constraints
- Concentrated Solar Power: location, location, location
- Why Concentrated Solar Power is not a good choice for a 100% Renewable Energy System
- Taxpayers are paying for a concentrated solar project — Ivanpah– that doesn’t work
- CSP with thermal energy storage is seasonal, so it can not balance variable power or contribute much power for half the year
6 Responses to Can concentrated solar power be used to generate industrial process heat?