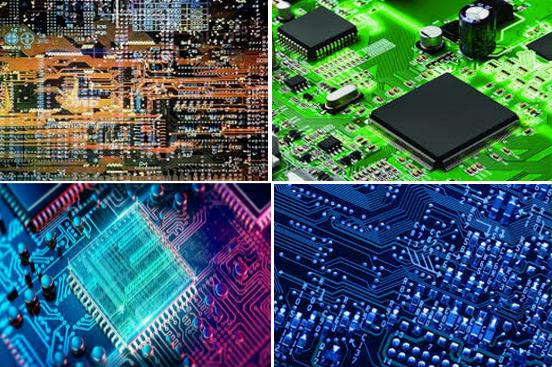
Preface. This is an introduction to how microchips are made to give you an idea of how difficult and amazing they are. This is a very high-level overview gathered mostly from the textbooks of Quirk (2001) and Van Zant (2004). Given the improvements since then, multiply whatever I say many fold as chips have only gotten more complex since them.
Alice Friedemann www.energyskeptic.com Author of Life After Fossil Fuels: A Reality Check on Alternative Energy; When Trucks Stop Running: Energy and the Future of Transportation”, Barriers to Making Algal Biofuels, & “Crunch! Whole Grain Artisan Chips and Crackers”. Women in ecology Podcasts: WGBH, Planet: Critical, Crazy Town, Collapse Chronicles, Derrick Jensen, Practical Prepping, Kunstler 253 &278, Peak Prosperity, Index of best energyskeptic posts
***
Microprocessors are essential, they’re in just about everything
Billions of chips are created every year for a myriad of applications: in autos, airplanes, ATMs, air conditioners, calculators, cameras, cell phones, clocks, DVDs, machine tools, medical equipment, microwave ovens, office and industrial equipment, routers, security systems, thermostats, TVs, VCRs, washing machines – nearly all electrical devices.
Microchip fabrication
Creating a chip begins by cutting a thin 12 inch slice, called a wafer, from a 99.9999999% pure silicon crystal, one of the purest materials on earth. Wafers require such a high degree of perfection that even a missing atom can cause unwanted current leakage and other problems in manufacturing later on. This is the platform that about 5000 computer chips will be built on. Each chip will contain millions of transistors, capacitors, diodes, and resistors built by punching and filling in holes in more layers than a Queen’s wedding cake.
Cleanliness
Particles 500 times smaller than a human hair can cause defects in microchips. The more particles that get on a wafer, the greater the chance there is of a killer defect. Some particles are worse than others — a single grain of salt could ruin all the chips on a wafer. Sodium can travel through layers even faster than stray bits of metal. Particles that outright kill a chip are caught during the testing phase at the factory. Sometimes only 20% make to the end. The traveling particles are insidious, and can cause a chip to malfunction, perform poorly, or die later on (hopefully before your warranty expires). Consumer reports recommends not even trying to repair a personal computer after four years, and in the two to four year range it’s a tossup whether to repair or buy a new one.
Typical city air has 5 million particles per cubic foot. There are processes that require a maximum of 1 particle per square cubic foot.
People are among the worst offenders, as far as particle generation goes. If you walk at a good clip, you emit 7.5 million particles per minute. Even sitting still, you are still emitting particles. A smoker is a particle-emitting dragon long after the cigarette, and a sneezing worker is even worse, a veritable Krakatoa.
City water is not pure enough to be used — it’s full of bacteria, minerals, particulates, and other junk. To make city water clean enough requires many filters, UV-light, and other water treatments. Intel has two plants in drought-stricken Arizona that use 11 million gallons of water a day and even more than that with a new expansion underway. This requires a huge investment in water processing and delivery systems.
Microchip fabrication is primarily a chemical process, requiring ultra-clean 99.9999% chemicals and 99.9999999% gases. About one in five steps use water or chemicals to clean the wafers or prepare their surface for the next layer.
Firemen practically need a chemical engineering degree to inspect and fight fires in a chip fabrication plant. During a fire, they risk being exposed to volatile, flammable, or combustible solvents, and chemicals like arsine, used in chemical warfare.
The chips also require humidity to be just right. If the humidity is too high, the wafers accumulate moisture, and the layers won’t stick. Too dry and static electricity will suck particles out of the air and practically glue them to the surface, they’re so hard to remove.
So it shouldn’t surprise you that it costs over billions of dollars to build a clean room. The inside is composed of non-shedding materials, especially stainless steel. Floors have sticky mats to pull dirt off of operators’ shoes. Pens, notebooks, tools, and mops – everything is built of material that sheds as few particles as possible, but even so, equipment particles cause a third of the contamination.
The slightest vibration can make the expensive machines malfunction, so the plant is built with huge concrete slabs on top of special shock absorbers. To make the foundation requires 890,000 cubic yards of dirt to be removed and dumped, then filled in with 445,000 cubic yards of concrete with 100,000 tons of embedded steel — more than required by the world’s tallest building, the burj Khalifa in Dubai.
It takes over 100 trucks to bring in the pieces of the huge cranes required for the project, which can life 55-ton chillers.
In order to move large amounts of liquids and gases, the plant needs to be very tall. Intel’s factories top level is 70 feet high to make room for giant fans to circulate air in the clean room below. Beneath the clean room there are thousands of transformers, pumps, cabinets, utility pipes, and chillers.
How chips are made
Wafers move from workstation to workstation and have different operations performed on them at each one. Wafer fabrication for a chip might involve 450 processes with operations that overall take several thousand individual steps. The machines that make this all happen include high-temperature diffusion furnaces, wet cleaning stations, dry plasma etchers, ion implanters, rapid thermal processors, vacuum pumps, fast flow controllers, residual gas analyzers, plasma glow dischargers, vertical furnaces, optical pyrometers, and more.
If you were shrunk to chip size and tied to a wafer, you’d go through the car wash from hell. You’ll be moved along by robotic wafer handlers from one machine to the next, where you’d be layered with different materials, centrifuged, electro-polished, dyed, scraped, heated to 1,800 degrees Fahrenheit, ultrasonically agitated, sputtered, doped, hard baked, dipped in toxic chemical baths, irradiated, blasted with ultrasonic energy, spray-cleaned, dry-cleaned, scrubbed, micro-waved, x-rayed, shot with metal, etched, and probed.
At various points, the chip “Survivor” TV show comes on. Chips are examined at an atomic level for defects, and their electrical functioning tested. They’re usually thrown out if anything is wrong, since most mistakes can’t be fixed.
There are many problems that can cause a chip to fail besides contamination. The wafer must be perfectly flat in structure and while it goes through the workstations. If the wafer were 10,000 feet high, you’d see bumps or holes no higher than 2 inches – more than that and the layering is thrown off. If the wrong step was performed after 3,841 correctly performed steps, the chip was under or overheated, the layer didn’t fully stick, was improperly aligned before the next layer was added, or a chemical misapplied, the chip is thrown out. It’s amazing any chips make it out the door.
After your makeover, you’d emerge in a designer outfit composed of up to 25 layers embedded with millions of transistors, diodes, and resistors. You’ll find yourself “best in show” at tattoo competitions and irresistible to Terminator fans.
Discussion
Chips are the pinnacle of human achievement, the most complex objects on earth, requiring fabrication plants costing ten billion dollars or more. They require chemicals, water, and air that are up to 99.99999999% pure. It takes thousands of steps and up to four months to process a wafer, all of them lost in an electricity outage.
Their precision is phenomenal. Before fossil fuels objects could be crafted to within a tenth of an inch. Today chips are created at an atomic level of precision.
They are also subject to a single point of failure. More than 90% of the world’s manufacturing capacity for the most advanced chips is in Taiwan, so any time Taiwan has a drought, earthquake, invaded by China, or can’t get the components needed for chips, the whole world is affected. And some of the machines that make chips are from just one factory. In Germany a fire impacted the only manufacturer making extreme ultraviolet lithography machines used to etch circuits onto silicon wafers for Apple, IBM, and Samsung and other companies (Koc 2022).
Microchips are constructed out of finite critical, precious, platinum group elements, and rare earth elements — 90% of them produced in China. And all of them mined with declining fossil fuels.
Chips have gotten so complex that their miniaturization has been causing hardware problems for over a decade. With switches just a few atoms wide, hardware failures that aren’t easy to identify are occurring more often. I don’t understand why chips work at all after reading this metaphor: Imagine a computer chip with 1,000 processors and 28 billion transistors is blown up to the scale of a building covering the United States. Finding the failure would be like finding the leaky faucet in just one of the apartments which only happens when the bedroom light is on and front door open.
There are trillions of tiny switches with billions of transistors in a microprocessor, so even a tiny imperfection can disrupt the billions of calculations taking place every second. About 4% of Google’s millions of computers crashed unexpectedly from errors that couldn’t be detected. A 2020 report by chip maker Advanced Micro Devices discovered the most advanced computer memory chips were 5.5 times less reliable than the previous generation. Other researchers say the switches are wearing out sooner and shortening the lifespan of processors.
Even really simple objects like pencils and toasters are more complex than you may know.
Microchips are incredibly important to civilization — like energy, there isn’t a single business endeavor, infrastructure, or electronic device that isn’t dependent on them.
New cars can have more than 100 semiconductors in their touch screens, computerized engine controls and transmissions, built-in cellular and Wi-Fi connections, collision avoidance systems, cameras and other sensors (Ewing and Clark 2021).
But because of their complexity, precision, dependency on rare minerals, supply chains, single points of failure, natural disasters, and extremely pure materials, they they will be one of the first industries to fail when the electric grid becomes unreliable and oil shortages become common, forcing society to simplify and localize, cascade to the myriad products that need them and making them obsolete as well.
Nearly all knowledge is being stored in electronically on media and devices that will be lost after energy decline, lost to the future generations forever, since fossil fuels and the mostly fossil-fueled electric grid make them possible. Books and microfiche have a finite lifespan as well, about 500 years if stored in optimal environments. I hope there are material scientists, librarians, and others working on more permanent media. And you can help as well by considering what knowledge you would like preserve, and how we could do so in “Peak Oil and the Preservation of Knowledge“.
The fragility of chips in the news:
Ting-Fang C et al (2021) Taiwan hit by triple blow of drought, blackouts and COVID surge
Zhong R et al (2021) Drought in Taiwan Pits Chip Makers Against Farmers. The island is going to great lengths to keep water flowing to its all-important semiconductor industry, including shutting off irrigation to legions of rice growers. New York Times: The drought is the worst in over half a century. Chip makers use lots of water to clean their factories and wafers, the thin slices of silicon that form the basis of the chips. Much of the water used by residents is deposited by the summer typhoons. But the storms also send soil cascading from Taiwan’s mountainous terrain into its reservoirs. This has gradually reduced the amount of water that reservoirs can hold.
References Much of above came from the textbooks written by Quirk & Van Zant
Clark D (2022) The huge endeavor to produce a tiny microchip. New York Times.
Ewing J, Clark D (2021) Lack of Tiny Parts Disrupts Auto Factories Worldwide. New York Times.
Koc C et al (2022) ASML keeps part of Berlin manufacturing site shut after fire. Bloomberg.
Markoff J (2022) Tiny Chips, Big Headaches. New York Times.
Quirk M, J. Serda J (2001) Semiconductor manufacturing technology. Prentice Hall.
Van Zant, P (2004) Microchip Fabrication, fifth edition. McGraw-Hill.
8 Responses to The Fragility of Microchips