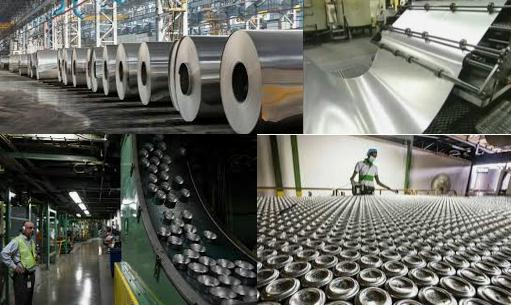
Preface. I am gobsmacked by how much energy goes into making beverage cans and potato chips, look at all the steps, each one using energy! Why haven’t we run of oil yet? Especially when you look at everything else out there, cars, roads, bridges, buildings, each of them going through even more energy intensive steps.
One of my ideas to preserve knowledge was to etch books on aluminum cans since they don’t rust and there are so many of them. Books and microfiche only last 500 years at best, and the electric grid will be down long before that. But with conventional oil peaking in 2018 (EIA 2020), there’s not much time left for my aluminum can preservation of knowledge, if it would work that is — the materials scientists I wrote didn’t write back. They probably still think I’m a crackpot!
EIA. 2020. International Energy Statistics. Petroleum and other liquids. Data Options. U.S. Energy Information Administration. Select crude oil including lease condensate to see data past 2017.
Alice Friedemann www.energyskeptic.com author of “Life After Fossil Fuels: A Reality Check on Alternative Energy”, 2021, Springer; “When Trucks Stop Running: Energy and the Future of Transportation”, 2015, Springer, Barriers to Making Algal Biofuels, and “Crunch! Whole Grain Artisan Chips and Crackers”. Podcasts: Collapse Chronicles, Derrick Jensen, Practical Prepping, KunstlerCast 253, KunstlerCast278, Peak Prosperity , XX2 report
***
Paul Hawken, Amory Lovins & L. Hunter Lovins. 1999. Natural Capitalism. Earthscan Publications Chapter 3: “Waste Not”, pages 49-50.
A striking case study of the complexity of industrial metabolism is provided by James Womack and Daniel Jones in their book Lean Thinking, where they trace the origins and pathways of a can of English cola. The can itself is more costly and complicated to manufacture than the beverage.
- Bauxite is mined in Australia,
- trucked to a chemical reduction mill,
- each ton of bauxite processed and purified into a half ton of aluminum oxide.
- It is then stockpiled,
- loaded on a giant ore carrier
- and sent to Sweden or Norway, where hydroelectric dams provide cheap electricity.
- After a month-long journey across two oceans, it usually sits at the smelter for as long as two months.
- The smelter takes two hours to turn each half ton of aluminum oxide into a quarter of a ton of aluminum metal, in ingots ten meters long.
- These are cured for two weeks before being shipped to roller mills in Sweden or Germany.
- There each ingot is heated to nearly 900 degrees Fahrenheit
- and rolled down to a thickness of an eighth of an inch.
- The resulting sheets are wrapped in ten-ton coils
- and transported to a warehouse,
- and then to a cold rolling mill in the same or another country,
- where they are rolled tenfold thinner, ready for fabrication.
- The aluminum is then sent to England,
- where sheets are punched and formed into cans,
- which are then washed,
- dried,
- painted with a base coat,
- and then painted again with specific product information.
- The cans are next lacquered,
- flanged (they are still topless),
- sprayed inside with a protective coating to prevent the cola from corroding the can,
- and inspected.
- The cans are palletized,
- fork lifted,
- and warehoused until needed.
- They are then shipped to the bottler,
- where they are washed
- and cleaned once more,
- then filled with water mixed with flavored syrup, phosphorus, caffeine, and carbon dioxide gas.
- The sugar is harvested from beet fields in France and undergoes
- trucking,
- milling,
- refining
- and shipping.
- The phosphorus comes from Idaho, where it is excavated from deep open-pit mines – a process that also unearths cadmium and radioactive thorium. Round-the-clock, the mining company uses the same amount of electricity as a city of 100,000 people in order to reduce the phosphate to food-grade quality.
- The caffeine is shipped from a chemical manufacturer to the syrup manufacturer in England.
- The filled cans are sealed with an aluminum ‘pop-top’ lid at the rate of fifteen hundred cans per minute,
- then inserted into cardboard cartons printed with matching color and promotional schemes.
- The cartons are made of forest pulp that may have originated anywhere from Sweden or Siberia to the old-growth, virgin forests of British Columbia that are the home of grizzly, wolverines, otters, and eagles.
- Palletized again, the cans are shipped to a regional distribution warehouse,
- and shortly thereafter to a supermarket where a typical can is purchased within three days.
The consumer buys twelve ounces of the phosphate-tinged, caffeine-impregnated, caramel-flavored sugar water. Drinking the cola takes a few minutes; throwing the can away takes a second. In England, consumers discard 84% of all cans, which means that the overall rate of aluminum waste, after counting production losses, is 88%. The United States still gets three-fifths of its aluminum from virgin ore, at 20 times the energy intensity of recycled aluminum, and throws away enough aluminum to replace its entire commercial aircraft fleet every three months.
Every product we consume has a similar hidden history, an unwritten inventory of its materials, resources, and impacts. It also has attendant waste generated by its use and disposal … The amount of waste generated to make a semiconductor chip is over 100,000 times its weight; that of a laptop computer, close to 4,000 times its weight. Two quarts of gasoline and a thousand quarts of water are required to produce a quart of Florida orange juice. One ton of paper requires the use of 98 tons of various resources.
Ryan JC, Durning AT. 2012. Stuff: The secret lives of everyday things. Sightline Institute.
A diesel-powered harvester dug up my potato, which was trucked to a processing plant nearby.
Half the potato’s weight, mostly water, was lost in processing.
The remainder was potato parts, which the processing plant sold as cattle feed.
Processing my potato created two-thirds of a gallon of waste-water. This water contained dissolved organic matter and one-third gram of nitrogen.
The waste-water was sprayed on a field outside the plant. The field was unplanted at the time, and the water sank underground.
Freezing the potato slices required electrical energy, which came from a hydroelectric dam on the Snake River.
Frozen foods often require 10 times more energy to produce than their fresh counterparts. In 1960, 92% of the potatoes Americans ate were fresh; by 1990, Americans ate more frozen potatoes, mostly french fries, than fresh ones. My fries were frozen using hydrofluorocarbon coolants, which have replaced the chlorofluorocarbons (CFCs) that harm the ozone layer. Some coolants escaped from the plant. They rose 10 miles up, into the stratosphere, where they depleted no ozone, but they did trap heat, contributing to the greenhouse effect.
A refrigerated 18-wheeler brought my fries to Seattle. They were fried in corn oil from Nebraska, sprinkled with salt mined in Louisiana, and served with ketchup made in Pittsburgh of Florida tomatoes. My ketchup came in four annoyingly small aluminum and plastic pouches from Ohio.
8 Responses to Many steps using fossil fuels to make cans & potato chips